A few years back, we were given a great opportunity. The east Texas field office of a United States gas company was interested in evaluating DIRAX. They had a relatively short (160 foot), 4.5" OD directional drilling application they were going to be carrying out and they were going to evaluate DIRAX sleeves; Cold Applied Tape and a Three Layer System similar to HTLP60.
Installations were completed based on manufacturer's recommended installation steps and the drill was begun. In this particular case, we were presented with a VERY interesting hiccup. Half way through the bore (meaning half way through the pipe's journey through the bore hole), there was a break down in equipment. As a result, the pipe had to be pulled out of the bore hole (backwards). At that point, the following photos and conclusions were reached:
 |
Cold Applied Tape after road bore attempt |
 |
Cold Applied Tape is MIA after road bore. |
A couple comments here. First, as you can see, the cold applied tape was not put on a field joint; it was instead installed on top of FBE (as can be seen in the picture). Second, this is not an attack on Cold Applied Tapes; I am not aware of any Cold Applied Tape manufacturer who claims their product should be used for a road bore application, so this is not a surprising result -- this is an expected result. Third, as can be seen, the Tape is completely gone (some threads of it still hang from the pipe in the bottom left section of the bottom picture.
Next is the Three Layer PE Sleeve system (similar to Covalence HTLP60). This product incorporates a liquid epoxy layer, a hot melt adhesive layer and a cross linked (but not fiber reinforced) PE backing. There are manufacturers out there who recommend, promote and sell products similar to this as a technically sound option for the field joint coating of road bore pipe.
 |
The three layer sleeve did not survive the road bore fully intact. |
 |
A close up of the result of the this three layer sleeves encounter with a rock or root during the bore. |
This product did do some things well, on the half way forward then back out journey. It stayed in place. It did not experience any wrinkling. It did not experience pull back or peel. Unfortunately, either on the way in...or the way out; this product did experience a collision with a rock or a root which resulted in a gouge being taken out of the coating. It is difficult to see here; but this gouge did reach the bare steel of the pipe.
To be clear, we would not recommend a simple three layer sleeve system like this one for a road bore or directional drilling application; for this exact reason. There are cases where a customer asks for an option that is more cost effective than the DIRAX, but we cannot in good faith offer a sleeve system like this. Compare the cost saved by using a cheap coating for a road bore with the cost of addressing a corrosion problem underneath a road a few years down the line...there is no comparison. Spending the money on the RIGHT coating now (DIRAX) will save tens of thousands of dollars down the road.
Finally we will look at our DIRAX sleeve. The DIRAX sleeve system consists of a liquid epoxy; a high shear hot melt adhesive and a mutli layer PE backing which includes a fiber reinforcement. The same sleeve material is then installed on the leading edge of the pipe (called a 'leader strip' or 'wear cone') which gives the most environmentally challenged piece of the shrink sleeve extra reinforcement during the pull through. As far as I know; the fact that this product was pulled backward out of the bore; without any kind of a leader strip in place was the first trial of its kind.
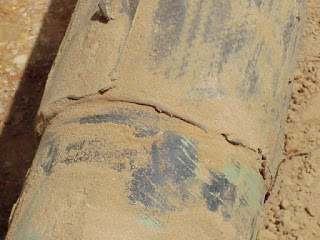 |
DIRAX is intact; compared to adjacent epoxy and FBE |
Above; we see the 'back end' of the DIRAX sleeve. This is the end that was supposed to have been reinforced with the leader strip. In this case, the DIRAX survived beautifully. The sleeve has not 'lifted up'. The dirt has not found its way under the sleeve. The DIRAX sleeve has not been torn; abraded or penetrated (the flap at the top left of the this picture is the closure strip - more on that below). In comparison, the FBE and the liquid epoxy (as seen just below the DIRAX) have experienced tremendous force. The liquid epoxy has been scratched completely away in several areas. It is difficult to tell; but the FBE (single layer) also experienced significant abrasion and damage.
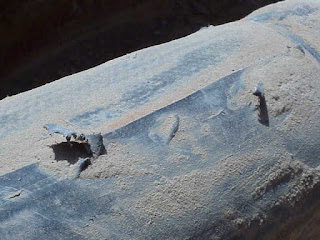 |
The closure strip has no corrosion coating responsibility. It's function is complete upon install. |
Here we see the only question that the Gas Company had about the DIRAX sleeve system. This is the closure strip (WPCPIV). Every wrap around shrink sleeve must use a closure strip of some kind. The closure strip is used to hold the sleeve in the shape of a tube during the shrink process. For the DIRAX (and other hot melt adhesive sleeves) the closure serves absolutely no purpose after the sleeve has been fully installed and the sleeve has cooled to ambient temperatures. In the picture above, we see two tears in the closure strip likely caused by a rock or root along the path. This damage did not effect the DIRAX sleeve underneath the closure. A force tough enough to tear through the cross linked closure strip had absolutely zero impact or effect on the DIRAX sleeve. Remarkable.
After this trial, the end user was convinced. It would be nothing but DIRAX on the field joints of road bored and directionally drilled pipe for them, and we had we had this field trial to thank for it.
No comments:
Post a Comment